History
The woodchipper was invented by Peter Jensen (Maasbüll, Germany) in 1884, the “Marke Angeln” soon became the core business of his company, which already produced and repaired communal- and woodworking–machinery.
Types
Disc
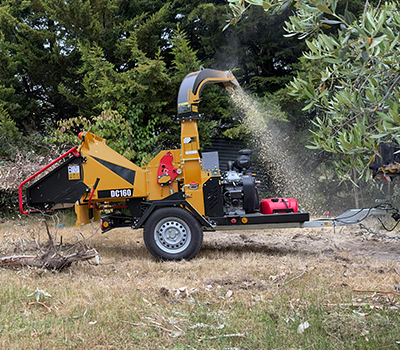
The original chipper design[2] employs a steel disk with blades mounted upon it as the chipping mechanism. This technology dates back to an invention by German Heinrich Wigger, for which he obtained a patent in 1922.[3] In this design, (usually) reversible hydraulically powered wheels draw the material from the hopper towards the disk, which is mounted perpendicularly to the incoming material. As the disk is turned by a motor, the blades mounted on the face of the disk cut the material into chips. These are thrown out the chute by flanges on the edges of the disk.
Commercial-grade disk-style chippers usually have a material diameter capacity of 15 to 45 cm (6 to 18 in). Industrial-grade chippers (tub grinders) are available with discs as large as 4 m (160 in) in diameter, requiring 3,000 to 3,700 kW (4,000 to 5,000 hp). One application of industrial disk chippers is to produce the wood chips used in the manufacture of particle board.
Drum
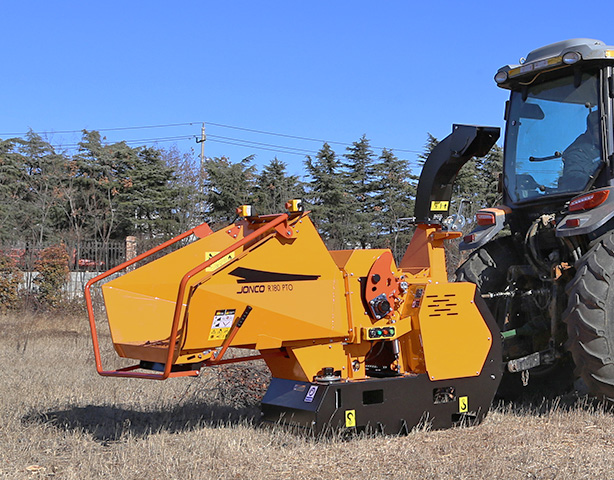
Drum chippers[4] employ mechanisms consisting of a large steel drum powered by a motor. The drum is mounted parallel to the hopper and spins toward the chute. Blades mounted to the outer surface of the drum cut the material into chips and propel the chips into the discharge chute. Commercial-grade drum-style chippers usually have a material diameter capacity of 25 to 60 cm (9 to 24 in).
Conventionally-fed drum chippers use the drum as the feed mechanism, drawing the material through as it chips it. These are colloquially known as “chuck-and-duck” chippers, due to the immediate speed attained by material dropped into the drum. Chippers of this type have many drawbacks and safety issues. If an operator becomes snagged on material being fed into the machine, injury or death is very likely. Hydraulically fed drum chippers have largely replaced conventionally-fed machines. These chippers use a set of hydraulically powered wheels to regulate the rate of feed of material into the chipper drum.
Other
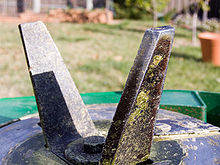
Much larger machines for wood processing exist. “Whole tree chippers” and “Recyclers”, which can typically handle material diameters of 60–180 cm (2–6 ft) may employ drums, disks, or a combination of both. The largest machines used in wood processing, often called “Tub or Horizontal Grinders”, may handle a material diameter of 2.4 m (8 ft) or greater, and use carbide tipped flail hammers to pulverize wood rather than cut it, producing a shredded wood rather than chip or chunk. These machines usually have a power of 150–750 kW (200–1,000 hp). Most are so heavy that they require a semi-trailer truck to be transported. Smaller models can be towed by a medium duty truck.
Blades
Although chippers vary greatly in size, type, and capacity, the blades processing the wood are similar in construction. They are rectangular in shape and are usually 4–10 cm (1+1⁄2–4 in) across by 15–30 cm (6–12 in) long. They vary in thickness from about 4–5 cm (1+1⁄2–2 in). Chipper blades are made from high grade steel and usually contain a minimum of 8% chromium for hardness.
City services
Fallen branches, especially when it is suspected that they are infested by beetles or their larva, are chipped to prevent further infestation. [5][1] City government acquires and operates chippers as needed,[6] including for seasonal use. [7]
Safety
Thirty-one people were killed in woodchipper accidents between 1992 and 2002 in the US, according to a 2005 report by the Journal of the American Medical Association.[8]
With development of technology and Safety directive standard, models being sold on market are safe if you follow the operator precedure.